
The pulse is active HIGH and the width of the pulse determines the position (angle) of the servos shaft. Servos expect to see a pulse on their PWM pin every 20mSec. This causes a high stall current condition and has the potential of stripping gears and damaging the motor, so it is best to either drive it to a safely reduced range such as 20-160 or experiment a bit to determine the actual usable range if you want to maximize the range. If the motor is run all the way to 0 or 180, it may start making unhappy sounds and start vibrating as it tries to drive to a position that it cannot get to.
Servo motor arduino turning a wheel full#
Frequently the actual range is not quite the full 180 degrees and is limited by the mechanical gears and potentiometer used for position sensing that is contained in the device. This is usually specified as 180 degrees. Standard servos have a specified limited range. Servo motors are comprised of a DC motor, gears, a potentiometer to determine its position and a small electronic control board. Servo motors can be commanded to go to a specific position and so are the usual go-to motor when accurate positioning is needed, such as for turning the front wheels on an RC model for steering or pivoting a sensor to look around on a robotic vehicle. Gears are nylon which is the case with most lower cost Servos. These servos work well for both servo experimentation as well as incorporation into many medium duty applications where its moderate size and good torque characteristics can be put to use. Strong, can lift 8lbs positioned 1cm from center of shaft.

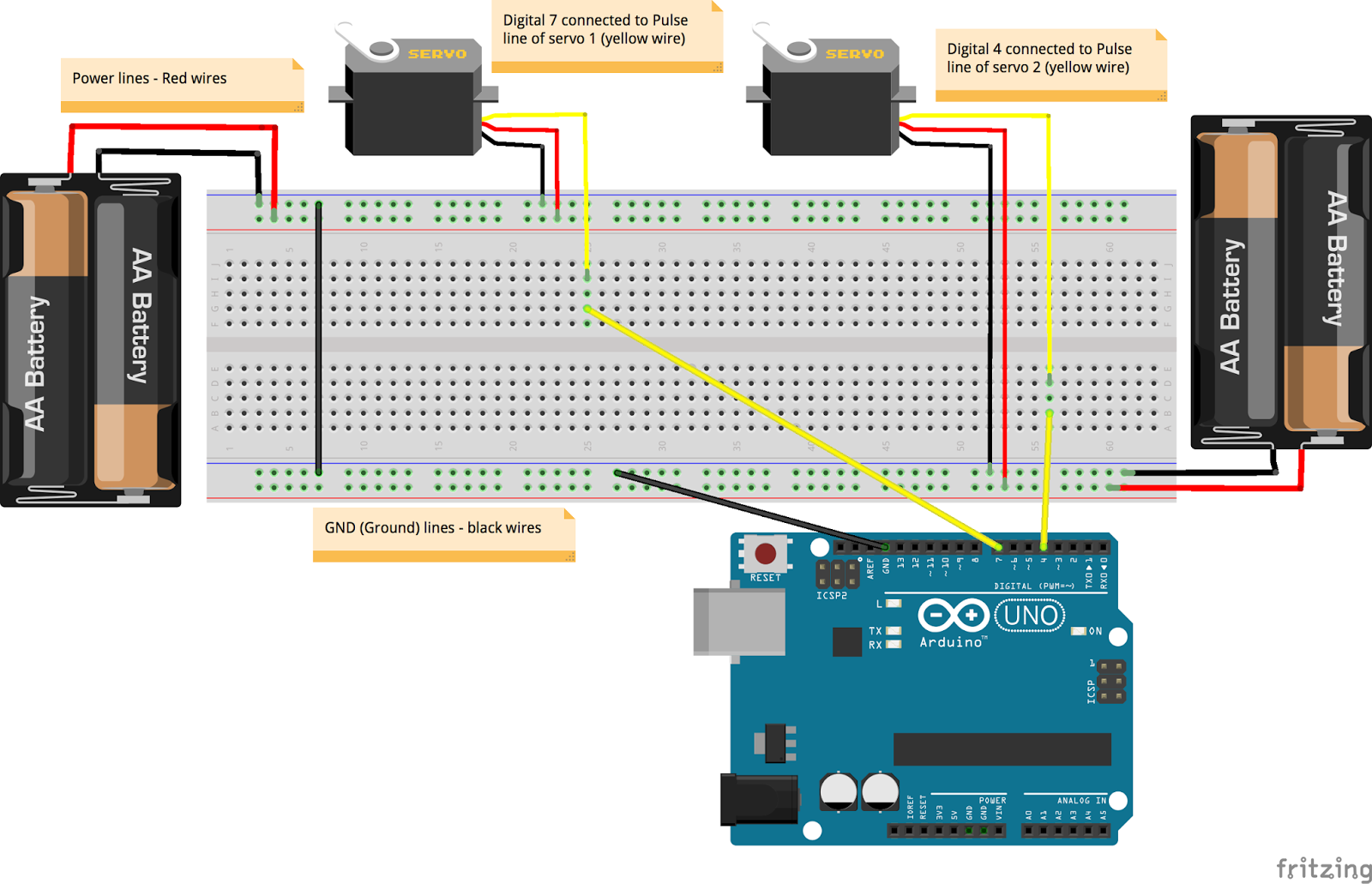
4 rubber and 4 brass bushings for mounting.Screws for mounting arms to the servo and mounting the servos.4 arms/horns for various interface applications.1 SG-5010 Servo motor with attached 9.5″ control cable.The Servo Motor SG-5010 is a workhorse standard servo with a range of 180 degrees that can be used in many applications and is one of the best values for a general purpose servo.
